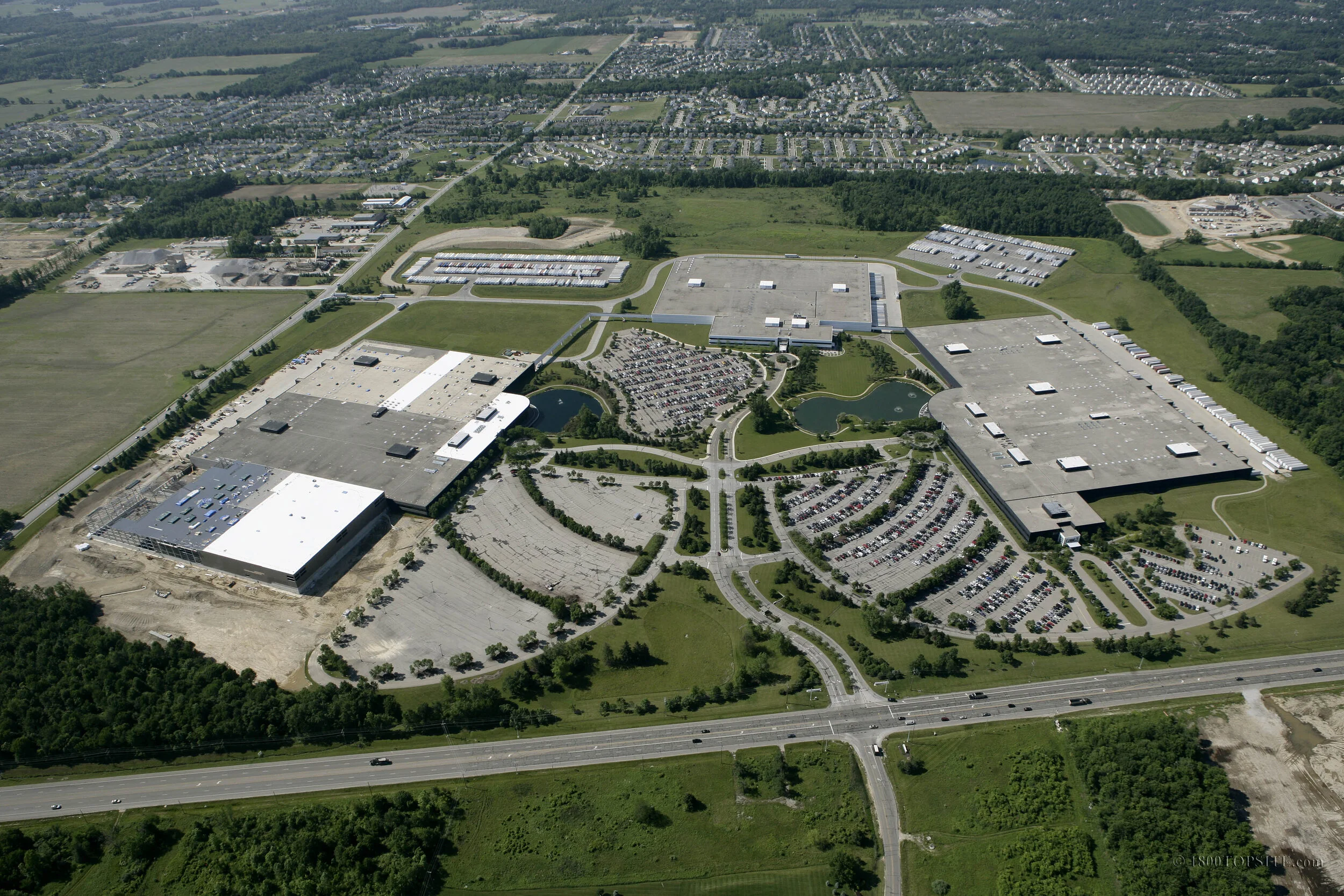
L Brands Distribution Centers
Location: Central Ohio
Size: 4 campuses: 832 acres total 9 buildings 1.4 Mil SF Office 5.7 Mil SF Distribution Center
Since 1974, when Acock Associates began work on the first corporate campus for Limited Inc., their philosophy regarding their facilities has been to design them in a way to be the most flexible and adaptable as possible. They wanted to make sure that their buildings could evolve and keep current with the latest trends in the retail industry.
Unlike most businesses, The Limited insisted that their distribution centers were constructed of the same high-quality materials as their office buildings, to reflect a similar image. They integrated large areas of windows in the exterior walls and installed numerous skylights to bring natural light into the space. The column bays and clear heights were maximized while the interior walls were kept to a minimum to provide the largest volume with the least amount of obstruction. The warehouse spaces were also outfitted with the same building systems as their corporate offices to maintain a consistent environment company-wide.
Over the next 50 years, the LBrand’s business interests diversified, and the various product lines ranged from women’s and men’s apparel, lingerie, personal care and beauty products to specialty retail and sporting goods. As technology has advanced, LBrand’s has also expanded their retail platform into e-commerce and direct to customer operations. Their physical facilities had also continued to grow to include 4 corporate campuses, totaling over 800 acres with 9 buildings and 5.7 million square feet of distribution center space.
The facilities also take advantage of incorporating different methods of fire protection in their buildings to provide additional flexibility in how things are stored, or the code required coverage for the various commodities being stored. As their beauty and personal care product lines became a larger part of their business, LBrands contracted UL to test storage and fire protection arrangements, specifically for their products, which by alcohol content are classified as flammable liquids. Upon successful testing they are now allowed to store those products in their distribution centers without having to separate them with fire barriers.
The built-in flexibility of their distribution centers allowed them to retrofit their existing buildings to allow them to employ the different storage arrangements and materials handling systems required to ship goods to their retail outlets. Along with their ever-changing business profile, they also continuously upgrade and employ the latest technology in materials handling equipment to improve their efficiency. The latest renovations have included Automated robotic retrieval systems, dramatically reducing the labor required as well as the time to fill orders.
This philosophy has allowed LBrands to evolve and adapt to keep pace with the ever-changing trends of the retail industry, while taking advantage of the latest in technology to improve their efficiency.
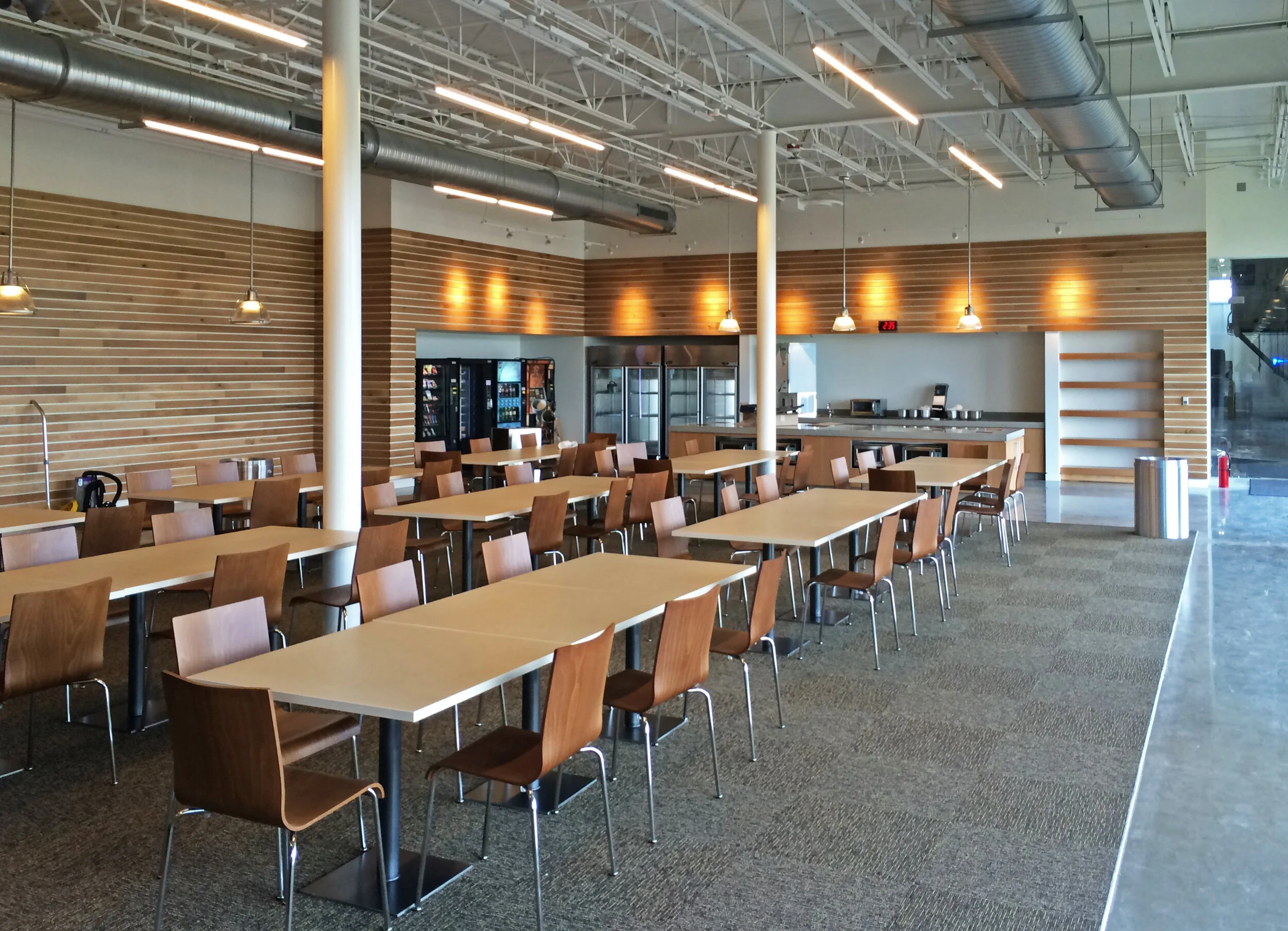